A new report from management consultancy Bain & Company suggests equipment manufacturers (EM) should focus on their battery strategies to meet the rising tide of sales.
Released on Wednesday, the report shows the global demand for battery strength is expected to quadruple to 4,100 gigawatt-hours (Gwh) between 2023 and 2030.
Lithium-ion batteries are set to remain the dominant technology for the foreseeable future, according to the report.
Despite emerging technologies like solid-state and high-density sodium-ion batteries making strides, they will likely continue to hold a small market share until 2030, as they are still in the prototype and pilot stages.
Additionally, nickel manganese cobalt (NMC) and lithium-iron phosphate (LFP) chemistries will lead the market.
Currently, these two chemistries represent over 90 per cent of lithium-ion battery sales for electric vehicles. In China, LFP will gain a larger share due to strong demand for mass-market EVs and well-established supply chains.
This dominance will be bolstered by new LFP variants such as M3P and lithium manganese iron phosphate (LFMP).
Conversely, LFP will gain market share in the United States and European Union. However, it will not not reach the levels seen in China. Factors such as limited domestic LFP production, less mature supply chains, and higher costs of importing LFP will impact its adoption.
In addition, advancements in no or low cobalt NMC variants, including NMx, high lithium manganese (HLM), and high-voltage mid-nickel options, may further diminish LFP’s cost advantage. Geopolitical issues and import tariffs might also challenge western EMs seeking to build more resilient supply chains.
Read more: Lithium South raises $4M in private placement
Read more: Lithium South and POSCO Holdings ink mutual development agreement
Technological advances will reduce cost of batteries
The technology will continue to advance, leading to reduced costs and enhanced performance. Significant innovations will include integrating the battery directly into the car’s chassis, adopting dry electrode manufacturing processes to cut energy consumption and costs, and utilizing AI-powered battery management systems to extend battery life.
“Batteries are the single biggest cost driver for EMs and they influence product performance. However, ongoing flux across battery chemistries, especially within lithium-ion batteries, are affecting EM product roadmaps,” said Mahadevan Seetharaman, a Bengaluru-based partner at Bain & Company’s Advanced Manufacturing Services practice.
“EMs across the world face the critical choice of which battery type to use and whether to develop batteries in-house or through collaboration with other companies.”
Solid-state and sodium-ion technologies are expected to emerge as the primary new options by 2030. Solid-state batteries offer higher energy density compared to NMC, along with improved safety, faster charging, and potentially longer life.
However, commercialization of solid-state technology is still three to four years away due to recent progress and previous delays. Sodium-ion batteries promise lower costs and better safety while operating at lower temperatures. However, their energy density has historically been lower.
Recent developments have improved sodium-ion performance, with commercial EVs anticipated to be available by early 2025.
The demand for recycling EV batteries is also set to grow significantly. Increased feedstock volumes and new global regulations on collection, recycling, and the use of recycled content will drive this trend. Battery manufacturers and EMs will explore new business models, such as battery rentals, to retain ownership and ensure responsible recycling.
.
Follow Joseph Morton on Twitter
joseph@mugglehead.com
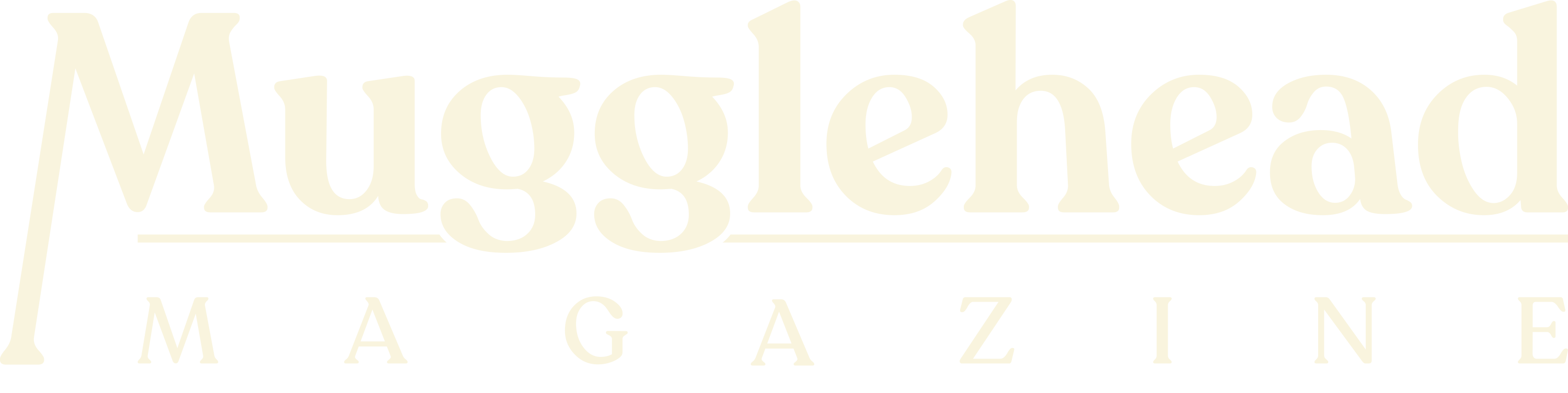