Defense Metals Corp. (TSXV: DEFN) (OTCQB: DFMTF) (FSE: 35D) has completed the work on its prefeasibility study, and it’s on schedule to be completed in Q2 2024.
On Tuesday, the company announced that its flotation pilot plant test work has produced high-grade mineral concentrate with 50 per cent Total Rare Earth Oxide (TREO) with an 80 per cent recovery rate.
The plant flowsheets for the PFS have been completed based on the metallurgical test work. Equipment specifications have been issued to vendors for cost quotations. Additionally, field-based geotechnical, geochemical, and environmental test work required for the PFS has been completed, and lab-based studies are currently under way.
Various other tasks for the PFS, including open pit mine design and tailings storage trade-off studies, are progressing well. Economic evaluation and cashflow modelling are also currently under way.
Furthermore, the bench-scale and hydrometallurgical pilot plant test work indicate that the planned acid bake process will yield approximately 90 per cent extraction of TREO from the mineral concentrate, resulting in a Mixed Rare Earth Carbonate product.
Over the past 5 years, Defense Metals has drilled 58 core holes totaling 12,073 meters to define the Wicheeda Rare Earth Element (REE) deposit and provide samples for metallurgical test work. This work has resulted in measured and indicated (M+I) resources of 34.2 million tonnes.
This represents a 260 per cent increase over the Defense Metals initial 2019 mineral resource estimate.
Total expenditures on the Wicheeda REE Project since 2019, including costs for mineral resource estimate definition, all metallurgical test work, earlier studies, and the remaining PFS-related costs, exceed CAD $17.5 million.
Read more: Idaho Strategic Resources discovers high grade rare earth elements in Idaho
Read more: Bacterial protein outperforms humans in separating rare earth elements: Penn State
Defense Metals allocates $5 million to metallurgical test work
Defense Metals performed a number of different tests to inform the PFS. Tests included developing and optimizing milling and hydrometallurgical processes. This also included analyzing the response of twenty-one variability samples representing different REE grades, lithologies, and locations within the deposit.
Since 2018, the company has allocated approximately CAD$5 million to metallurgical test work and developing metallurgical flowsheets for the Wicheeda REE Project. Part of this involves detailed mineralogical examinations. which the company conducted on thirty-one samples of deposit material, flotation, and hydrometallurgical products.
“Continuing positive results from our technical studies suggest that our wholly-owned Wicheeda REE Project has the potential to become the next producer of rare earth elements in North America accounting for a significant amount of the rare earths needed for the western world’s future magnet metal production,” Craig Taylor, CEO of Defense Metals, said.
Defense Metals also conducted sixty-three static acid bake tests, as well as sixteen short-duration acid bake kiln runs with associated water leach tests. Additionally, SGS completed a total of 15 days of continuous kiln operation. This was part of a fully integrated hydrometallurgical pilot plant operation that processed 560 kg of flotation concentrate.
The company performed approximately 40 bench-scale impurity removal tests, along with about 40 rare earth precipitation tests. The company then integrated the results into the hydrometallurgical pilot plant operation and the project process design criteria.
Various small-scale tests explored water recycle options and other aspects of the metallurgical flowsheets.
Read more: Saskatchewan develops proprietary extraction cells for rare earth processing facility
Read more: New Tesla motor could disrupt rare earths sector
REE are vital for modern technology
Rare earth elements are a group of 17 chemical elements that have unique properties. Those properties make them essential in a wide range of modern technologies.
REEs find diverse applications in modern technology, including manufacturing of high-strength permanent magnets used in electric vehicle motors, wind turbines, and various electronic devices such as headphones, speakers, and hard disk drives.
Additionally, REEs serve as catalysts in industrial processes, including petroleum refining, automotive catalytic converters, and chemical manufacturing. Also, In the realm of lighting and display technology, certain REEs like europium and terbium are indispensable for creating phosphors used in LED lights, fluorescent lamps, and television screens.
.
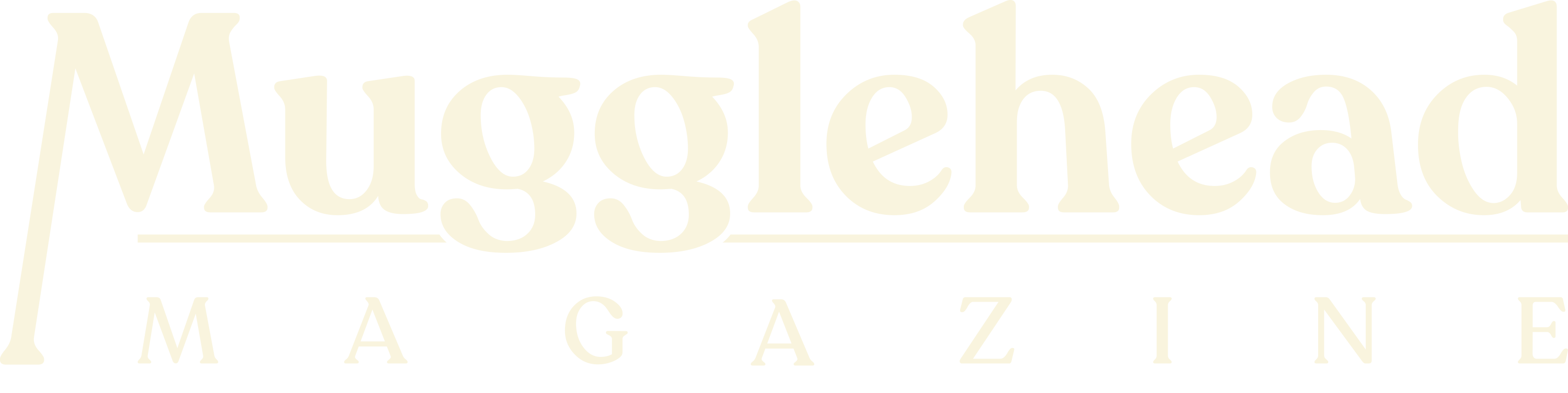